L’obiettivo è creare una NUOVA LINEA DI ASSEMBLAGGIO che migliori l’efficienza riducendo i tempi di set-up aumentando la produttività e ottimizzando il flusso dei materiali. L’analisi si basa su una revisione del processo condotta presso il Cliente e propone un piano di riorganizzazione della linea di assemblaggio basato sui principi Kaizen.
Analisi dello Stato Attuale
L’attuale situazione della Linea di Assemblaggio è caratterizzata da diverse inefficienze, tra cui:
- Tempi di set-up eccessivi: la linea richiede un cambio di set-up completo per ogni ordine di produzione, con 80 set-up all’anno. Ogni set-up coinvolge tre operatori e richiede 4,5 ore, per un totale di 360 ore annue;
- Alti livelli di inventario: il processo di assemblaggio presenta un inventario significativo di Work-In-Progress (WIP), con materiali sparsi lungo la linea;
- Movimentazione inefficiente dei materiali: gli operatori impiegano molto tempo a cercare parti e a trasportare materiali;
- Muda: vengono eseguite diverse attività che non aggiungono valore, come la gestione degli imballaggi e dei materiali di scarto;
- Problemi ergonomici: gli operatori provano disagio a causa della posizione non ergonomica dei materiali e della necessità di sollevare prodotti pesanti.
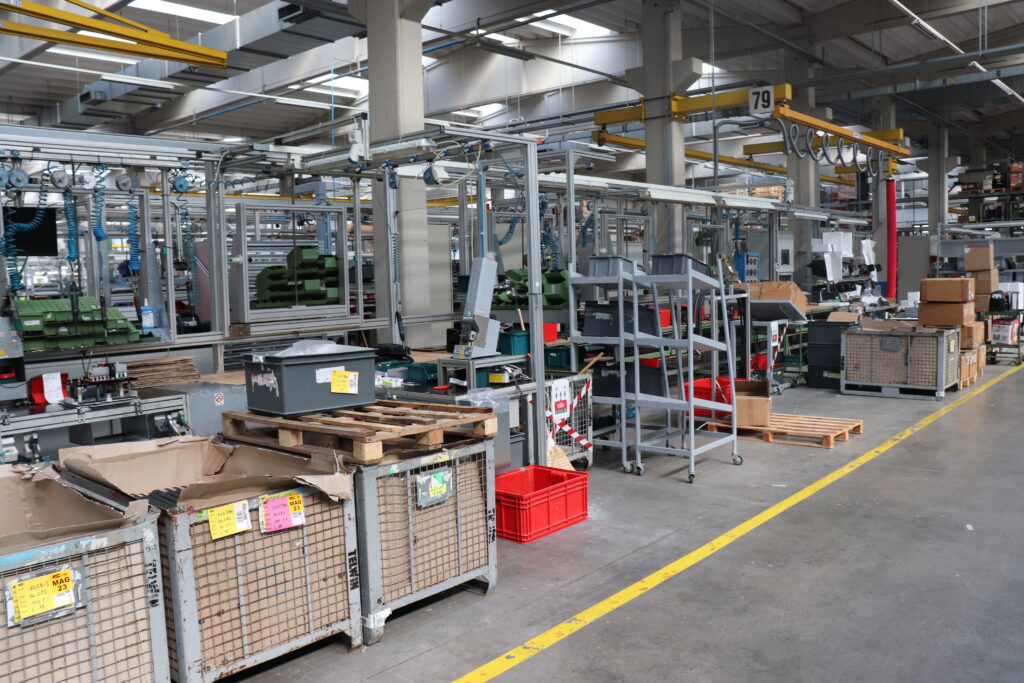
Piano di Miglioramento e messa in opera di una linea di assemblaggio a 3 operatori
Il piano di riorganizzazione proposto per la Linea di Assemblaggio si concentra su tre fasi principali:
Fase 1:
- Implementazione delle 5S: implementare le 5S (Separare, Sistemare, Splendere, Standardizzare, Sostenere) per creare un ambiente di lavoro pulito, organizzato ed efficiente;
- Miglioramenti alla sicurezza: migliorare la sicurezza delle postazioni di lavoro attraverso una migliore organizzazione e la standardizzazione dei processi;
- Introduzione del sistema Pull: introdurre un sistema pull per controllare il flusso dei materiali e ridurre l’inventario WIP;
- Miglioramenti ergonomici: potenziare l’ergonomia delle postazioni di lavoro per ridurre l’affaticamento e lo sforzo degli operatori, riducendo così gli infortuni;
- Implementazione del sistema Kanban: implementare un sistema Kanban per segnalare la necessità di rifornire i materiali.
Fase 2:
- Implementazione dello SMED: applicare i principi del Single-Minute Exchange of Die (SMED) per ridurre drasticamente i tempi di set-up;
- Kitting e Supermarket: creare un supermercato con kit pre-assemblati di parti, semplificando la gestione dei materiali e i cambi di set-up;
- Logistica Just-in-Time: implementare un processo logistico Just-In-Time basato sul principio del “Chirurgo e Infermiere”, garantendo la consegna tempestiva dei materiali;
- Ottimizzazione del Milk Run: migliorare l’efficienza del Milk Run eliminando la gestione di contenitori vuoti per materiali voluminosi ed eliminando la presenza del carrello elevatore dalla produzione;
- Picking Standardizzato: standardizzare le attività di Picking utilizzando liste di prelievo e organizzazione a supermercato.
Validazione applicazione nuove metodologie e logiche di asservimento con l’azienda.
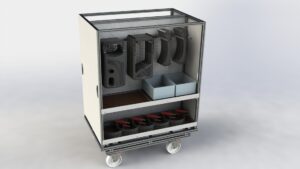
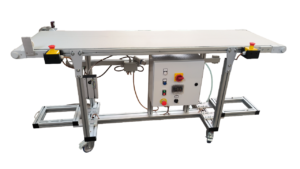
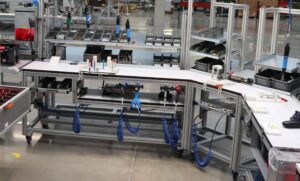

Fase 3:
La nostra azienda progetta utilizzando SolidWorks, che è lo strumento indispensabile per realizzare progetti di elevata complessità e che ci consente di visualizzare e analizzare l’intero processo produttivo in 3D.
- Progettazione delle postazioni di lavoro con implementazione logica Kanban per il materiale minuteria;
- Progettazione dei carrelli Kitting utilizzabili con il sistema Milk Run;
- Progettazione e creazione del nastro trasportatore
- Integrazione nel progetto di tutti i prodotti dell’ergonomia per Picking e movimentazione materiale;
- Approvazione del progetto completo ed eventuali cambiamenti di dettagli tecnici.
Tutto il processo di produzione, viene effettuato all’interno della nostra sede e i nostri prodotti sono modulari e concepiti per garantire una facile riconfigurabilità.
Riepilogo dei Risultati
La tabella sottostante riassume i miglioramenti ottenuti da prima e dopo l’implementazione del piano di riorganizzazione:
Metrica | Prima del Miglioramento | Dopo il Miglioramento | Miglioramento (%) |
Tempo di Setup (ore/anno) | 360 | 60 | 83,3% |
Produttività (unità/anno) | 7097 | 7558 | 6,5% |
Rischio Ergonomico (movimenti disagevoli, con movimenti del tronco molto ampi) | 33% delle attività di prelievo | 0% | +∞% |
I risultati ottenuti dimostrano il potenziale per ottenere significativi miglioramenti in termini di produttività, qualità e benessere dei lavoratori attraverso l’implementazione di metodologie Lean Manufacturing.
Le linee di assemblaggio Kaizen Key sono il nostro punto di forza, in quanto la collaborazione tra le nostre due Business Unit genera un valore aggiunto al processo produttivo.
Vuoi aumentare l’efficienza della tua azienda? Contattaci per fissare un incontro conoscitivo!
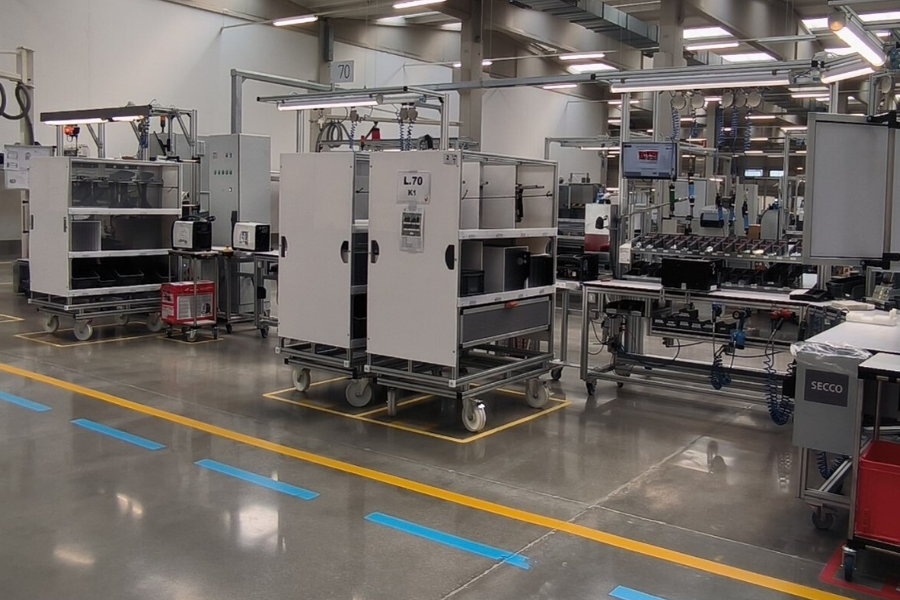